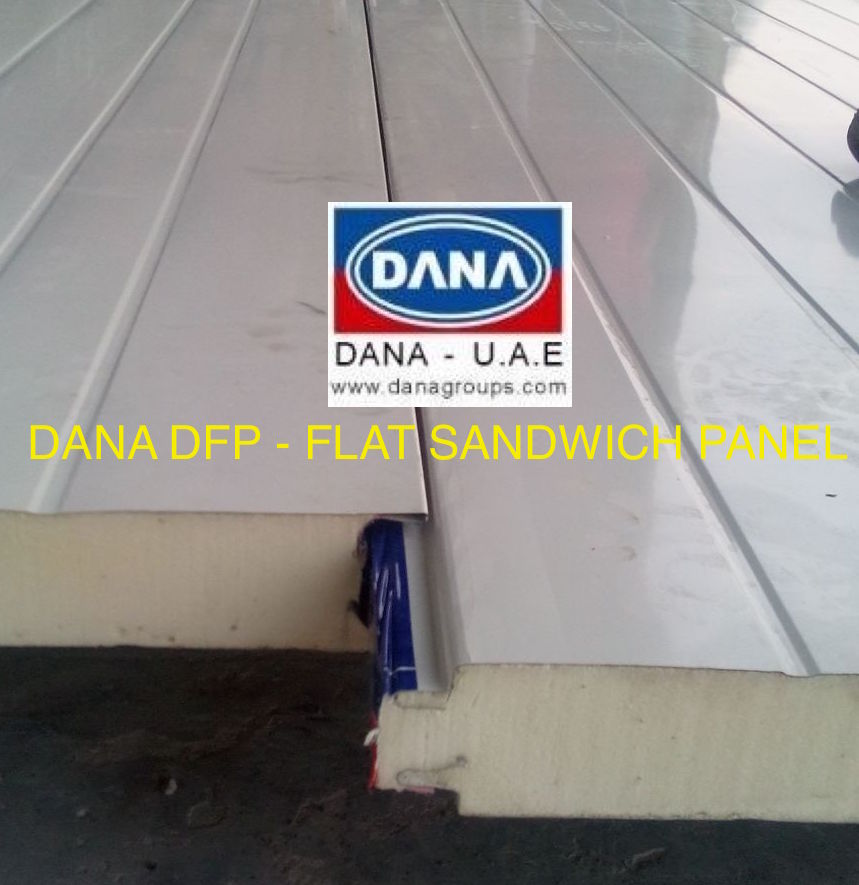
Panels are delivered in packages, each of them consisting of a certain number of piled-up panels. A panel with a foam core is easy to handle and can cope with large spans, and even a relatively thin core produces high insulation values. Note: faces of sandwich loaded by normal stress, axially if have solid material loaded axially, want to maximize E=ˆ core loaded in shear and in the foam, cell edges bend if have solid material, loaded as beam in bending and want to minimize weight for a given sti ness, maximize E. Sandwich panel SPA corner element FLASHINGS 100. The faces and the core of the sandwich panel are adhesively joined in order to transfer the load between the components. This provides a structure which is very efficient for resisting bending and buckling loads since the sandwich panel is much stronger and stiffer, in most respects,.
Such panels comprise thin facings which are secure usually by adhesive bonding, to a relative thick, low-density core material. This complements approximately twenty years experience of testing external cladding systems. Other applications present different degrees of risk of inception and fire spread. Here, we describe a method for making square honey-comb sandwich cores from super-austenitic stainless steels and use it to construct large sandwich panels with a core relative density of around 5–.
The honeycomb core consists of sinusoidal wave corrugations and straight components sandwiched between the facings. The sandwich panels usually absorb impact energy using two different mechanisms, namely, local crushing and global bending. A sandwich panel consists of a porous low-density core, e. This product, made with the use of advanced production processes, offers optimal performance of the designed solution. Low U-value and proper joint design together with wide thickness range make this sandwich panel an ideal solution for cold storage buildings.

Wall sandwich panels PU by Europanels were designed to fulfill several functions. The most important are: resistance to atmospheric factors, thermoinsulation, aesthetics, durability, functionality and versatility. The continuous core is an additional advantage, which improves aesthetic of the building. A typical sandwich panel consists of two surface plates and the core. The panels are made mainly from synthetic materials (composites) or metals (aluminium, steel).
The structure of sandwiches can differ depending on the type of core elements and the method of joining them to surface plates. Some examples of the structure of sandwich panel are presented in Figures and 2. New data for sandwich panels on the correlation between the SBI test method and the room corner reference scenario, Fire and Materials. Report on Experimental Programme and Recommendations. A schematic illustration of the basic concept is shown in Fig. The top and bottom of the sandwich are sheets of duralumin alloy about mm.
Precast sandwich panels are typically made of an external concrete layer (non-load bearing), an insulation layer and an internal concrete layer (load bearing). Special connectors placed during casting are connecting those three layers. Basing on a great experience in the area of determination of the fire resistance class of construction building elements the authors describe the properties and behavior of building elements made of the sandwich panels exposed to fire.
The sandwich panel widely used as roof, wall and garage door in modern construction specifiers go to the sandwich panel due to high standard in thermal insulation, quick and easy installation and variety of colors. Tempcon sandwich panels are produced using rigid Polyisocyanurate (PIR) foam core with external and internal sheets in steel or aluminum of varying thickness, coatings and colors. Tempcon is a durable sandwich panel , particularly in industrial buildings and are suitable for roof and wall for all building applications.
No comments:
Post a Comment
Note: Only a member of this blog may post a comment.