The wear-out period is characterized by a rapid increasing failure rate with time. In most cases this period encompasses the normal distribution of design life failures. Quiz time… TRUE or FALSE.
The types of maintenance management are. No actions or efforts are taken to maintain the equipment as the designer originally intended to ensure design life is reached. Predictive maintenance is the complement of preventive maintenance.
Through the utilization of various nondestructive testing and measuring techniques, predictive maintenance determines equipment status before a breakdown occurs. Periodic maintenance ( Time based maintenance - TBM) 2. Four general types of maintenance philosophies can be identifie namely corrective , preventive , risk-based and condition-based maintenance. Companies (SMEs as well as large groups) know how their productivity partly depends on their industrial maintenance processes. Five types of maintenance are in fact recurrent in the industry: corrective, preventive, condition-base predictive and predetermined.
The maintenance workforce lacks either the discipline or direction to follow best maintenance repair practices 4. Standard scheduled maintenance is further divided into three types of checks called ‘A Checks’, ‘C Checks’ and ‘D Checks’. There are types of maintenance activities: 1. This strategy may be cost - effective until catastrophic faults occur. Maintenance personnel do not have the requisite skills 3. Adaptive maintenance is concerned with the change in the software that takes place to make the software adaptable to new environment such as to run the software on a new operating system. Such a thing could be used when the equipment failure does not significantly affect the operation or production or generate any significant loss other than repair cost.
Corrective maintenance is concerned with fixing errors that are observed when the software is in use. Their is mechanical preventive maintenance and electrical preventive maintenance. Mechanical looks at failure of bearings, wear plates, shims and etc…. Electrical looks at the failure of motors,.
Prevention is always the prime objective of management. But in case of high cost production systems, there are several limitations with breakdown maintenance. In this type of maintenance , the maintenance activities are planned well in advance to avoid random failure. Clean end of grease gun 3. Chapter looks at the different types of maintenance programs and definitions.
Lubricate with proper amount and right type of lubricant. Chapter focuses on maintenance technologies, particularly the most accepted predictive technologies. Transformer Oils (continued) 6. Moisture Problems (continued) 6. Department of Energy’s Federal Energy Management Program (FEMP). Reactive maintenance (breakdown maintenance) Also known as breakdown or run-to-failure, reactive maintenance is pretty simple: fix things when they break.
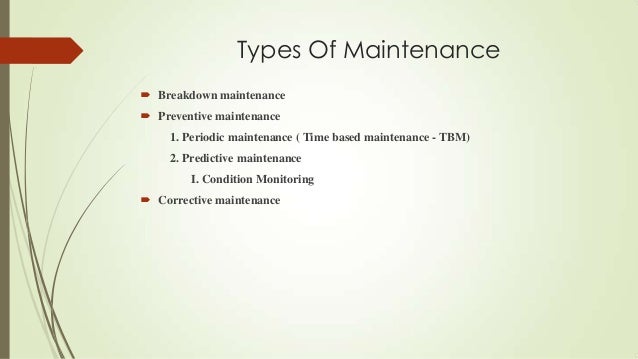
Since repairs are not planne it’s a good method to employ for equipment that is not essential for operations or has a low cost (think anything that’s rarely used or duplicates the function of other equipment). Preventive maintenance is limited to the maintenance organization only and no external requests are acquired for this type of maintenance. Author: Abasaheb Sangle.
No comments:
Post a Comment
Note: Only a member of this blog may post a comment.